1. Einen soliden ROI erzielen
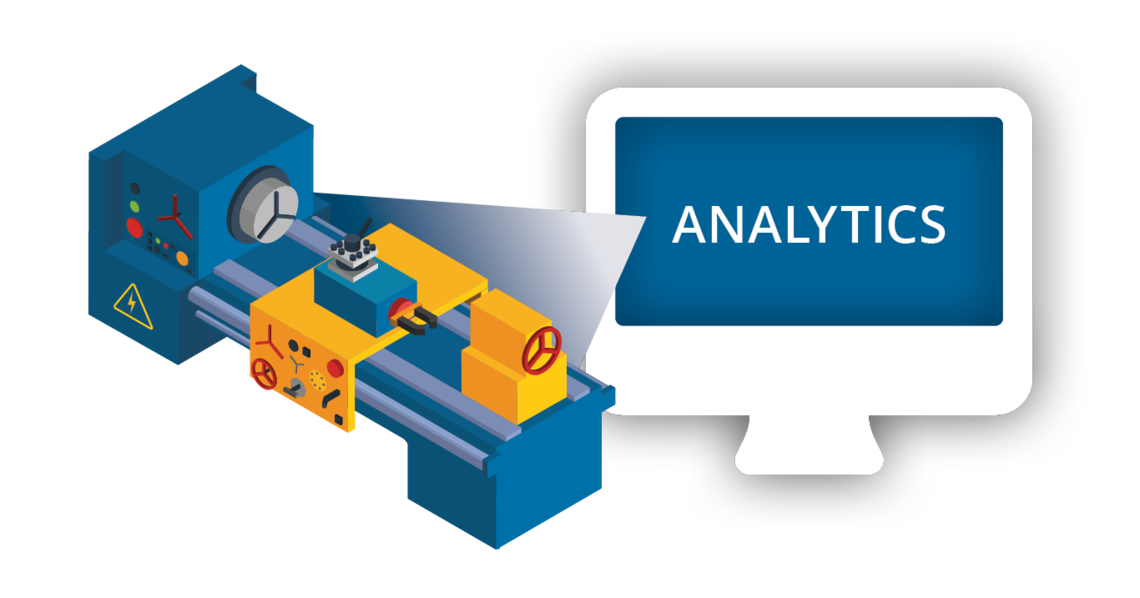
Angesichts der Breite und Tiefe der Digitalisierung in der diskreten und in der Prozessfertigung verfolgen viele Unternehmen in der ersten Phase einer IIoT-Implementierung einen schrittweisen Ansatz: Durch einzelne POCs oder die selektive Nachrüstung vorhandener Anlagen und Maschinen mit intelligenten Sensoren können Hersteller den Nutzen von IIoT-Analysen für konkrete Anwendungsfälle evaluieren und etwaige Folgeinvestitionen in anderen Geschäftseinheiten abwägen.
- Erträge steigern
- Betriebskosten senken
- Rentabilität verbessern
2. Die Produktionsleistung maximieren
Wenn die Produktion auf ein Industrie 4.0-Niveau gebracht wurde und die Anlagen und Maschinen durchgängig Leistungsdaten generieren, kann ein Hersteller von einem reaktiven zu einem proaktiven Ansatz vorausschauender Instandhaltung übergehen. Durch die Echtzeitüberwachung des Maschinenparks, der Produktionsleistung und der Anlagenintegrität werden Leistungsabfälle sichtbar, bevor eine kritische Ressource versagt. Darüber hinaus muss sich die Reparaturplanung nicht mehr nach der mittleren fehlerfreien Betriebszeit (MTBF / Mean Time Between Failures) richten, sondern berücksichtigt den tatsächlichen Zustand der jeweiligen Anlage bzw. Maschine.
- Ungeplante Stillstände reduzieren
- Technische Probleme vorhersehen
- Ursachen identifizieren
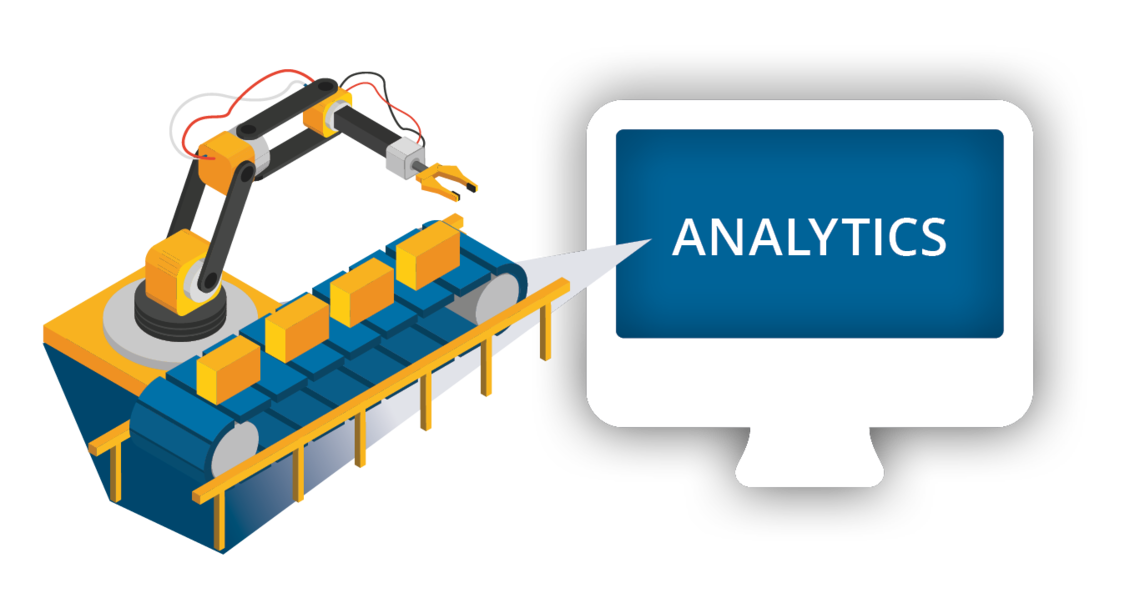
3. Die Qualität konstant halten
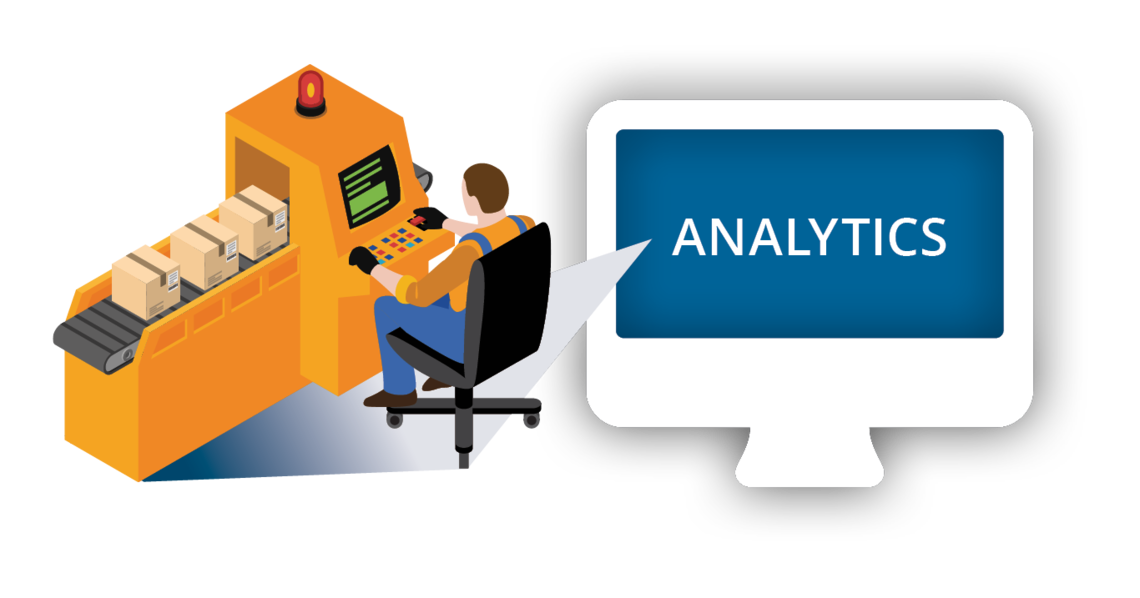
Durch die kontinuierliche Überwachung auch der geringsten Abweichungen bei Temperatur, Durchfluss, Druck und anderen Parametern können Techniker und andere verantwortliche Mitarbeiter Produktionsfehler erkennen bzw. verhindern und sogar Anpassungen bei laufenden Chargenprozessen vornehmen. Mit Echtzeit-Datenvisualisierung und -analysen werden Störungen bereits im Ansatz erkennbar gemacht.
Ein fehlerhafter Fertigungsprozess kann sich in nur einer Minute auf Hunderte oder Tausende von Produkten auswirken, die Erstausbeute (First Pass Yield) reduzieren und die Stückkosten nach oben treiben. Dank Echtzeit-Warnmeldungen für die Überschreitung von Grenzwerten, Toleranzen oder anderen Vorgaben können rechtzeitig Korrekturmaßnahmen eingeleitet und damit die Schwankung oder Nichtkonformität der Produktionsergebnisse verringert werden.
- Produktionsfehler erkennen und vermeiden
- Zuverlässigkeit der Anlagen steigern
- Produktionsausfälle reduzieren
4. Die Effizienz steigern
Von der Steigerung der Anlagenverfügbarkeit, des Produktionsertrags und der Durchsatzmenge bis hin zur Reduzierung von Ausschuss, Abfall und Nacharbeiten können Hersteller den Produktionszyklus optimieren. Eine umfassende Erfassung von Produktionsdaten sorgt jedoch nur dann für Effizienzvorteile, wenn diese Daten wertsteigernd verwertet werden können.
Mit intelligenten Sensoren können in Echtzeit große Mengen an Daten wie Temperatur, Gewicht, Zeitstempel usw. erfasst werden. Die kontinuierliche Analyse dieser Daten kann minimalste Schwankungen in den Prozessen und Anlagen aufzeigen, die anhaltende Qualitätsprobleme, Produktionsverluste oder sogar Maschinenausfälle zur Folge haben können.
- Ausschuss reduzieren
- Erstausbeute (First Pass Yield) steigern
- Anlagenverfügbarkeit erhöhen
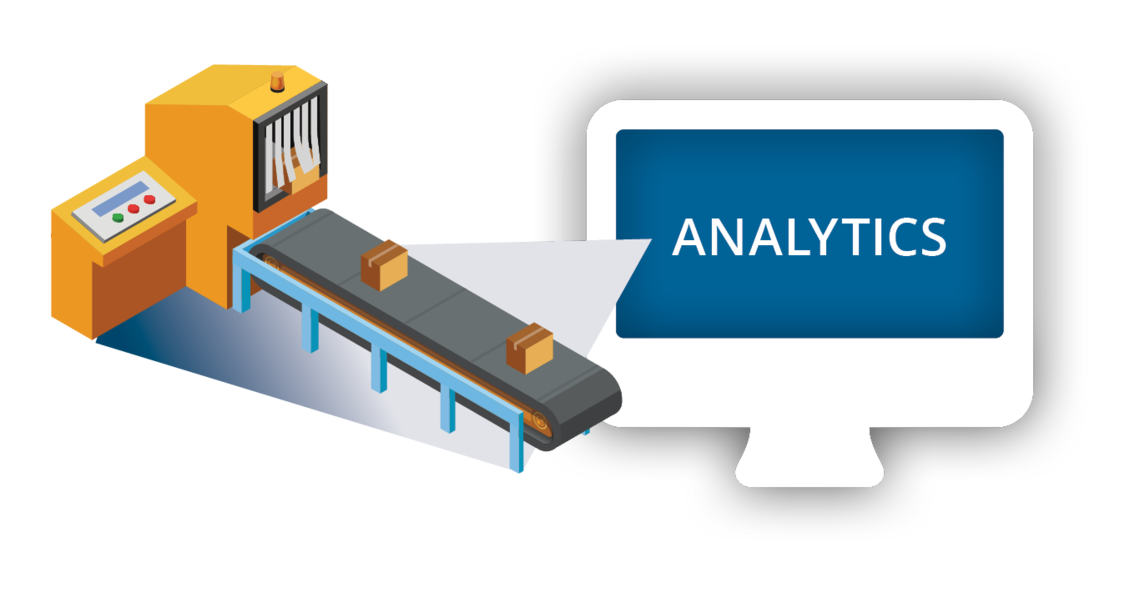
5. Eine bessere Compliance erreichen
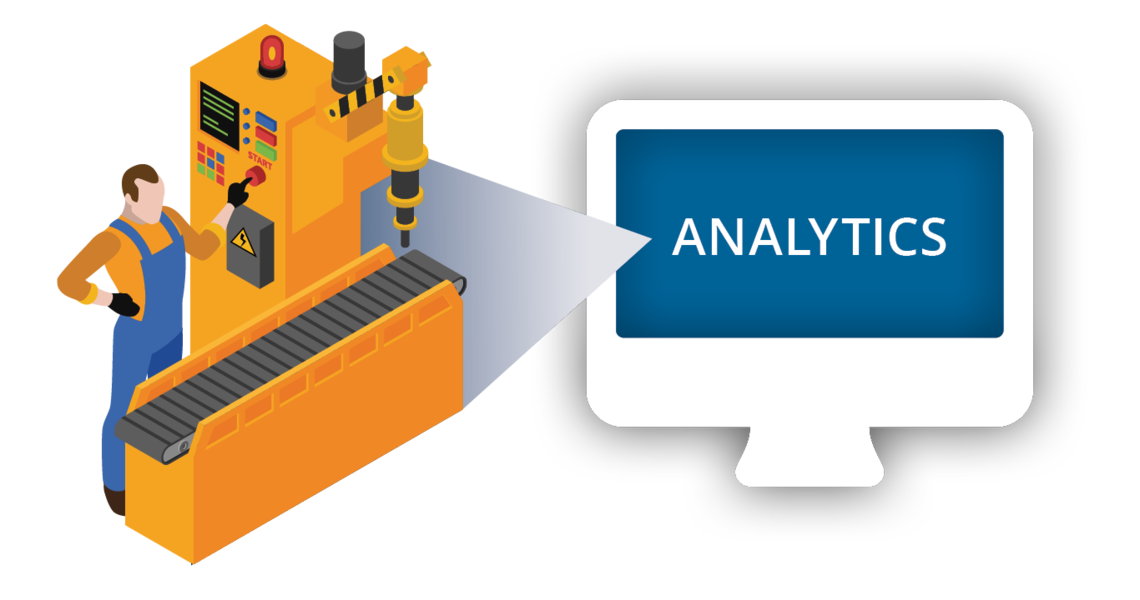
- Korrekte/fehlerhafte Arbeitsweise von Maschinen und Anlagen beurteilen
- Sicherheitsbedingte Ausfälle reduzieren
- Sicherheitsrisiken eindämmen
Obwohl Industrie 4.0 in erster Linie die Produktivität und Effizienz optimieren soll, können die Daten von Maschinen und Anlagen auch zu einer Verbesserung der Arbeitssicherheit beitragen. Bediener und Techniker können anhand von M2M-Daten (Machine to Machine) feststellen, wo, wie lange und wie oft in der Werksumgebung unsichere Arbeitsbedingungen vorherrschen und entsprechende Vorkehrungen treffen, um die Einhaltung von Arbeitsschutzvorschriften zu gewährleisten.
Im Fertigungsbereich können Fehlercodes, Zeitstempel und Systemwarnungen über den gesamten Maschinenpark abgestimmt werden, wodurch die Ursachen von Arbeitsunterbrechungen, Anlagenausfällen und sicherheitsbedingten Abschaltungen besser nachvollziehbar werden.
Industrie 4.0-Analysen implementieren
Produktionsanalysen liefern das fehlende Teil im Industrie 4.0-Puzzle und sind gleichsam die „letzte Meile“ zwischen den Betriebsabläufen in der Werkshalle und der Entscheidungsfindung in der Führungsetage. Die möglichen Vorteile von Industrie 4.0-Lösungen in den Bereichen ROI, Produktionsleistung, Qualität, Effizienz und Compliance lassen sich nur dann realisieren, wenn Unternehmen Plattformen für Produktionsanalysen einsetzen, die praxisrelevante und nachvollziehbare Ergebnisse liefern.
Geeignete Plattformen für wertschöpfende Produktionsanalysen sind eine sinnvolle Ergänzung zu etablierten SCADA-, MES- und ERP-Systemen. Hinsichtlich Funktionsumfang und Implementierungsaufwand unterscheiden sie sich jedoch deutlich von diesen Lösungen.
Ihr Weg zur Industrie 4.0
Die umfassende Realisierung von Datenanalysen in der industriellen Fertigung ist zweifellos eine gewaltige Aufgabe, doch selbst kleine Fortschritte und Erfolge auf dem Weg in Richtung Industrie 4.0 werden mit deutlichen Verbesserungen von Produktivität, Qualität und Effizienz belohnt. Zukunftsorientierten Herstellern bietet sich die Möglichkeit, durch die kontinuierliche Weiterentwicklung und schrittweise Verbesserung ihrer Systeme und Prozesse die operativen Abläufe von einem reaktiven auf einen proaktiven Ansatz umzustellen.
Unabhängig davon, in welchem Stadium der Entwicklung zur Industrie 4.0 sich Ihr Unternehmen gerade befindet: Der zentrale Aspekt ist und bleibt die Schaffung von Effizienzgewinnen auf jeder Produktionsstufe – von der Erfassung, Archivierung und Visualisierung von Anlagen- und Maschinendaten bis hin zur kontinuierlichen Echtzeitüberwachung und einer fortlaufenden Analyse der Produktionsleistung.
Wenn Sie mehr über die Implementierung einer Produktionsanalyse-Lösung in Ihrer IT und/oder OT sowie die damit verbundenen technischen Anforderungen erfahren möchten, setzen Sie sich mit Intelligent Solutions in Verbindung und fragen Sie nach der EDM-Lösung für Produktionsanalysen, oder vereinbaren Sie einen Termin für eine Live-Online-Präsentation.
Fünf Gründe, warum Hersteller Echtzeitanalysen implementieren sollten
Lernen Sie unsere Industrie 4.0-Lösungen näher kennen!